3D Printing Revolution: From Prototyping to Mass Production
In the dynamic landscape of modern manufacturing, 3D printing stands out as a transformative technology. Once relegated to the realm of prototyping, 3D printing has now evolved into a robust tool capable of mass production. This article explores the revolutionary journey of 3D printing, highlighting its impact on various industries and its potential for the future.
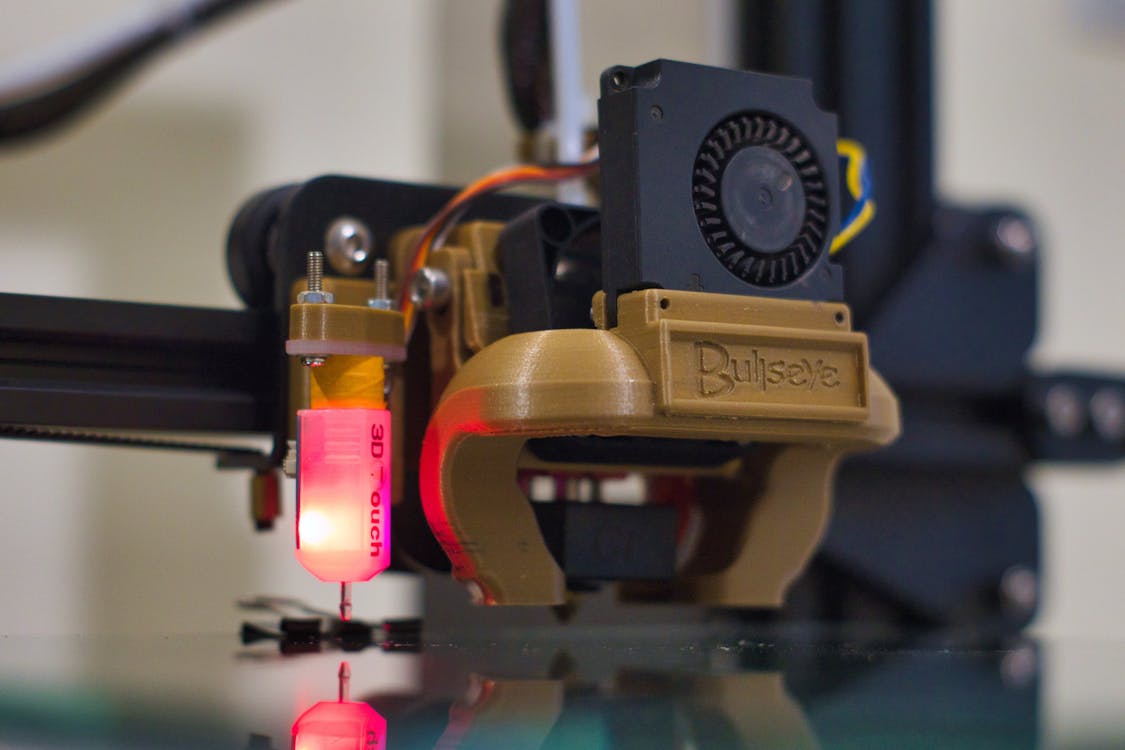
The Evolution of 3D Printing
3D printing, also known as additive manufacturing, began as a method to create prototypes quickly and cost-effectively. Early adopters hailed its ability to produce detailed models directly from digital designs, which significantly accelerated the design iteration process. Today, the capabilities of 3D printing extend far beyond prototyping, encompassing a wide array of applications from aerospace to healthcare.
Prototyping: The First Step in 3D Printing
In its initial stages, 3D printing was primarily used for prototyping. Engineers and designers leveraged this technology to create physical models from CAD files. This rapid prototyping allowed for quick testing and refinement of design concepts without the need for expensive and time-consuming traditional manufacturing methods.
The advantages of 3D printing for prototyping are numerous:
Speed: Prototypes can be produced in a matter of hours.
Cost: Reduces the need for specialized tools and molds.
Flexibility: Allows for easy modifications and iterations.
Transition to Production: The Turning Point
As 3D printing technology matured, its application began to shift from merely creating prototypes to producing final products. Innovations in materials and advancements in printing techniques played crucial roles in this transition. High-performance thermoplastics, metals, and composites are now commonly used in 3D printing, making it possible to produce durable, end-use parts.
Key Industries Embracing 3D Printing for Production
Aerospace: The aerospace industry benefits greatly from 3D printing due to its ability to produce lightweight, complex components. For example, GE Aviation uses 3D printing to manufacture fuel nozzles for jet engines, resulting in parts that are 25% lighter and five times more durable than traditionally manufactured components.
Healthcare: Customized medical devices, such as implants and prosthetics, are now commonly produced using 3D printing. This technology allows for patient-specific solutions, improving outcomes and reducing recovery times. In some cases, bioprinting is used to create tissue and organ structures, potentially revolutionizing transplants and regenerative medicine.
Automotive: The automotive industry utilizes 3D printing for both prototyping and production. Companies like BMW and Ford use 3D printing to create tools, fixtures, and even production parts, reducing lead times and costs while enhancing design flexibility.
The Future of 3D Printing in Mass Production
As 3D printing continues to evolve, its role in mass production is becoming more pronounced. The technology offers several advantages that are particularly appealing for large-scale manufacturing:
Customization: Mass customization becomes feasible, allowing manufacturers to produce unique products tailored to individual customer specifications.
Sustainability: Additive manufacturing is inherently less wasteful than traditional subtractive methods, aligning with global sustainability goals.
Supply Chain Efficiency: On-demand production can reduce inventory costs and lead times, making supply chains more responsive and resilient.
Challenges and Considerations
Despite its many benefits, 3D printing faces challenges that must be addressed to fully realize its potential in mass production:
Material Limitations: While the range of printable materials is expanding, there are still limitations in terms of strength, durability, and cost.
Speed: Although 3D printing is faster than traditional prototyping methods, it is still generally slower than conventional mass production techniques.
Quality Control: Ensuring consistent quality in mass-produced 3D printed parts can be challenging, requiring rigorous testing and validation processes.
Conclusion
The journey of 3D printing from prototyping to mass production marks a significant milestone in manufacturing innovation. As technology continues to advance, the potential applications of 3D printing will only grow, offering new possibilities for efficiency, customization, and sustainability. For businesses and industries willing to embrace this revolution, the future holds exciting opportunities to redefine how products are designed, produced, and delivered.
By staying at the forefront of 3D printing advancements, companies can leverage this powerful technology to gain a competitive edge and drive the next wave of industrial transformation.
You have not logged in, please Login to comment.